Top Benefits of Metal Presswork in Automotive Manufacturing
In the world of automotive manufacturing, precision and efficiency are incredibly important. With the increasing demand for high-quality, durable, and cost-effective parts, manufacturers must rely on advanced techniques that can meet these needs while supporting sustainability goals. One such technique is metal presswork, a critical process used to produce high-precision components at scale.
Metal presswork, or metal stamping services, play a central role in transforming raw materials into essential automotive parts, from intricate body panels to structural components. This manufacturing process offers a range of benefits, including speed, precision, and the ability to produce complex shapes with minimal waste. Whether it's for mass production or the creation of lightweight materials that enhance fuel efficiency, metal presswork has become a cornerstone of the modern automotive industry.
In our blog, we’ll explore the top benefits of metal presswork in automotive manufacturing, highlighting how it drives innovation, cost savings, and sustainability within the industry. From precision metal pressing to material efficiency, we’ll uncover how this technique continues to shape the future of automotive production. To learn more, keep on reading.
What is Metal Presswork?
Metal presswork is the process of using a mechanical press to shape or cut metal into desired forms. This is typically done by placing metal sheets into a press machine that applies high pressure to create specific shapes and features. The process involves various techniques, such as stamping, forming, embossing, and blanking, depending on the complexity of the parts being produced.
In automotive manufacturing, metal presswork is an essential part of creating a wide range of components, from the body panels of vehicles to intricate parts in the engine and suspension systems. The process can involve various metals, including steel, aluminium, and high-strength alloys, which are chosen based on the specific requirements of the part being produced.
There are also different types of metal presswork, which includes progressive stamping, deep drawing, and piercing. Each of these processes plays a vital role in producing parts that require complex geometries and tight tolerances, such as automotive body parts, interior components, and structural elements.
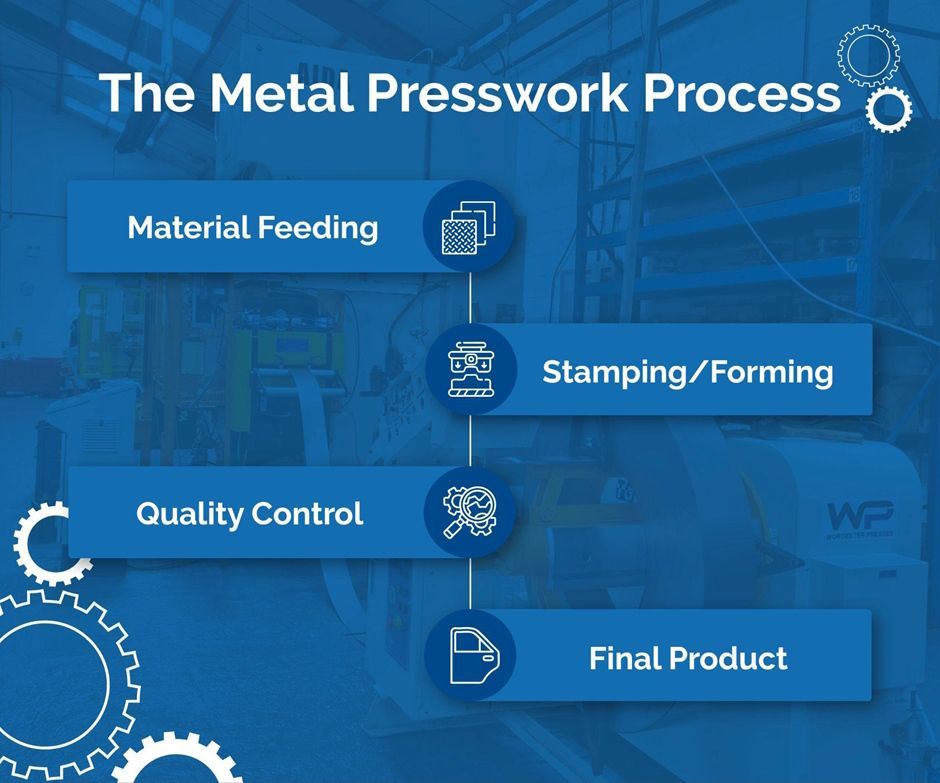
Understanding Key Benefits of Metal Presswork in Automotive Manufacturing
High-Speed Production
One of the main advantages of metal presswork is its ability to produce parts quickly and efficiently. The speed of the process makes it a great solution for mass production within the automotive industry. The ability to produce high volumes of parts in a short amount of time allows manufacturers to meet demanding production schedules and deliver products just in time (JIT) to assembly lines.
This high-speed production capability means that automotive manufacturers can scale up their operations to meet high demands, reducing lead times and improving the overall supply chain efficiency. With automated press machines, manufacturers can achieve rapid turnaround times without having to compromise on quality.
Precision for Complex Parts
Metal presswork offers a level of precision that is difficult to match with other manufacturing techniques. The ability to form metal into complex shapes with tight tolerances is crucial in automotive manufacturing, where even the smallest mistakes in part dimensions can lead to issues during assembly or performance.
Presswork enables the production of parts with intricate specifications, such as body panels with curves and bends, or engine components with precise features like holes and slots. This precision is achieved through sophisticated press machines and tooling, ensuring that every part meets the exact specifications required for its intended purpose. For example, parts like door panels, engine mounts, and even structural chassis components benefit from the ability to form complex shapes consistently and accurately.
Consistency and Quality Control
Metal presswork is known for its ability to remain consistent across large production runs. Once a tool or die has been set up in the press, it can produce identical parts with very little variation. This consistency is essential for making sure that automotive parts meet strict quality standards and perform as they should in the final assembly.
By using automated presses and advanced monitoring systems, manufacturers can easily track the quality of parts being produced. Any deviations from the desired specifications can be detected and corrected immediately, reducing the risk of defective parts reaching the assembly line. This level of control ensures that automotive manufacturers can maintain high levels of quality without having to conduct extensive manual inspections.
Scalability for Mass Production
Scalability is another major benefit of metal presswork. The ability to scale production easily and efficiently makes it an ideal choice for many automotive manufacturers who need to produce large quantities of parts at competitive prices.
Once the necessary dies and tooling are set up, the process can be scaled to produce hundreds or even thousands of identical parts without any additional effort. This is particularly beneficial in the automotive industry, where manufacturers need to produce large volumes of components for vehicles. Whether it’s a single part or a series of parts across multiple vehicle models, metal presswork can handle the demand with ease, making it an attractive option for large-scale production runs.
Material Efficiency and Waste Reduction
In addition to the benefits of speed and precision, metal presswork is also an environmentally friendly option for automotive manufacturers. The process allows for material efficiency, as it makes sure that as little material as possible is wasted during production. Techniques like progressive stamping and nesting are also particularly effective in maximising material usage, reducing scrap and lowering your production costs.
In fact, many automotive manufacturers are increasingly turning to presswork as a way to reduce waste and lower their overall environmental footprint. By minimising material waste and recycling scrap metal, presswork contributes to a more sustainable manufacturing process, aligning with the automotive industry’s sustainability goals.
Supporting Lightweighting Strategies
The push for lightweighting in automotive manufacturing is another area where metal presswork plays a pivotal role. As automakers strive to meet fuel efficiency and emissions regulations, reducing the weight of vehicles has become a key focus. Metal presswork allows for the creation of lightweight, high-strength parts that are incredibly important for these efforts.
By using materials like aluminium and high-strength steel, metal presswork can produce components that are both strong and light, which helps manufacturers reduce the overall weight of vehicles without sacrificing their durability or safety. The ability to precisely form these materials ensures that they meet the necessary performance standards, while also contributing to improved fuel efficiency and lower emissions.
The Role of Metal Presswork in Sustainability
Sustainability is increasingly important in the automotive industry, and metal presswork supports these efforts in multiple ways. Not only does the process reduce material waste, but it also plays a role in energy efficiency. The precision of metal presswork ensures that each part is made with minimal energy consumption, as fewer resources are wasted during production.
Additionally, scrap metal generated during the presswork process is usually recycled, which reduces the need for raw materials and lowers the environmental impact of production.
Cotmor Tool & Presswork: Metal Fabrication &
Metal presswork offers a wide range of benefits for automotive manufacturing, from high-speed production and precision forming to material efficiency and sustainability. Whether it’s enabling lightweighting strategies or supporting mass production, this technique continues to drive innovation and cost savings in the automotive industry.
For manufacturers looking to optimise their production processes, metal stamping services and precision metal pressing can provide the edge they need to stay competitive. As the industry continues to evolve, metal presswork will remain an essential part of the automotive manufacturing landscape, delivering high-quality, reliable components that meet the needs of today’s market.
Looking for metal pressing services? Cotmor Tool & Presswork is a reliable metal pressing manufacturer, offering a range of services for both small and large scale requirements. Get in touch with us to learn more about how we can help you.