Advantages and Applications of MIG Welding in Manufacturing
At Cotmor Tool and Presswork, we understand that welding is the backbone of modern manufacturing. From car bodies to construction frameworks, welding creates the strong, lasting bonds that industries rely on. Different welding techniques suit different requirements, but few are as versatile, efficient and widely used as MIG welding.
With decades of experience producing precision metal assemblies and metal fabrications, we have seen first-hand how MIG welding has transformed manufacturing. In this article, we explore what MIG welding is, its advantages, its applications and why Cotmor remains a trusted name for expert welding services across the Midlands and the wider UK.
What Is MIG Welding?
MIG welding, or Metal Inert Gas welding, is a type of Gas Metal Arc Welding (GMAW) that uses a continuous solid wire electrode fed through a welding gun. At the same time, a shielding gas is delivered through the nozzle to protect the weld pool from atmospheric contamination.
The shielding gas, usually a mixture of argon and carbon dioxide, ensures a cleaner, stronger weld. The continuous wire feed acts as both the electrode and filler material, making the process faster and more efficient than many other welding methods.
MIG welding is well suited to a wide range of metals, including mild steel, stainless steel and aluminium. Its simplicity and speed make it the go-to choice for high-volume manufacturing and precision metal fabrications.
At Cotmor, our skilled welders use MIG techniques daily, combining technical expertise with modern equipment to deliver the highest quality results.
Key Advantages of MIG Welding in Manufacturing
MIG welding offers numerous benefits that make it ideal for manufacturing environments where speed, reliability, and flexibility are essential. Here are some of the key advantages:
Speed and Efficiency
Because MIG welding uses a continuously fed wire and requires less frequent stops to change rods or clean slag, it is much faster than methods like stick welding.
For manufacturers needing to produce large volumes of metal parts or assemblies, this speed leads directly to lower production costs and quicker turnaround times.
Versatility
MIG welding can be used on a broad range of metals and varying thicknesses. Whether you're working with thin aluminium sheets or heavy steel frames, MIG welding can be adapted with the right filler materials and shielding gases.
This versatility is crucial in industries like automotive, construction and engineering, where diverse projects require flexible solutions.
Ease of Use
Compared to TIG welding, MIG welding is easier to learn and operate. The welder can concentrate on guiding the torch rather than manually feeding filler material, which reduces the margin for error and shortens training times.
At Cotmor, we value techniques that promote both quality and efficiency - and MIG welding offers exactly that.
Strong, Reliable Joints
MIG welding produces clean, consistent welds that provide excellent strength. It’s suitable for structural and load-bearing applications, making it perfect for critical components in metal assemblies and machinery frames.
Minimal Post-Weld Cleaning
Unlike stick welding, which generates a lot of slag that must be chipped away after welding, MIG welding produces far less spatter. This means less time spent cleaning and finishing the welded area, contributing to faster production cycles.
At Cotmor Tool and Presswork, we maximise these advantages to deliver high-quality welding services that meet demanding industry standards - and exceed client expectations.
Applications of MIG Welding in Manufacturing
The practical advantages of MIG welding mean it’s found across a wide range of industries. Here are some of its most common applications:
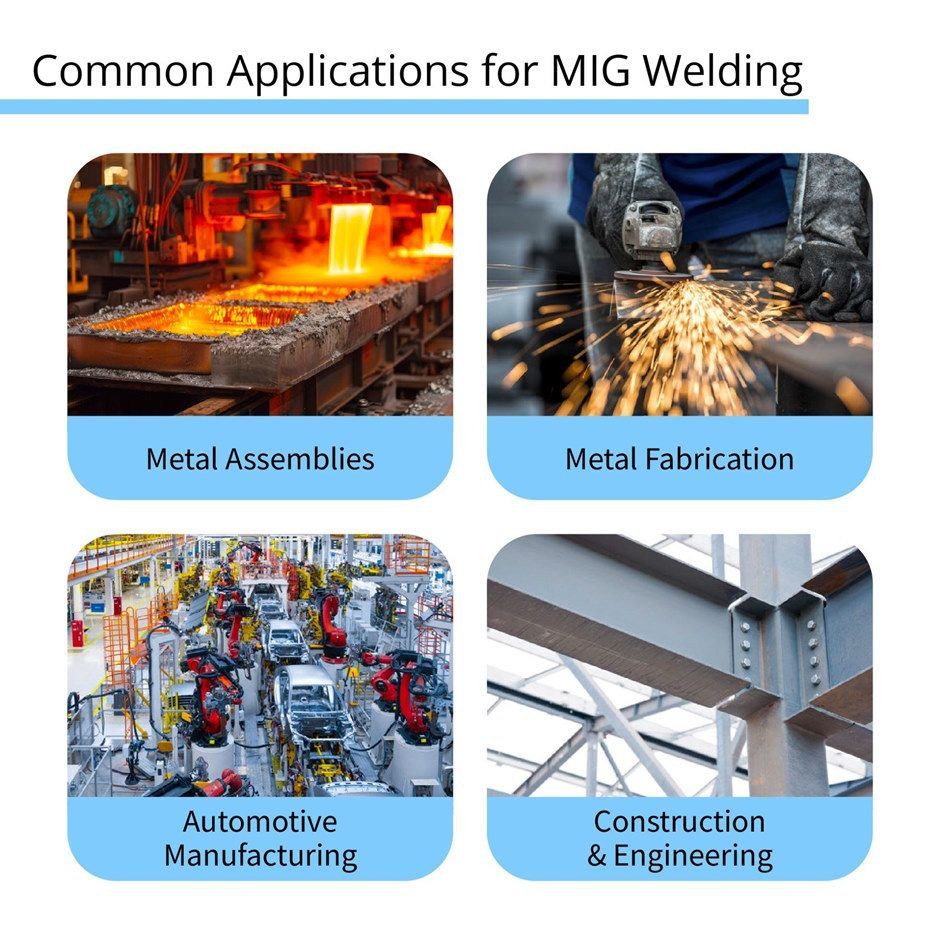
Metal Assemblies
MIG welding is frequently used in the creation of metal assemblies, where multiple components must be joined with strength and precision. These assemblies could be machine parts, structural supports, or custom mechanical frameworks.
Our team at Cotmor regularly produces metal assemblies for customers in automotive, manufacturing, and construction industries.
Metal Fabrications
When fabricating frames, brackets, panels, or custom enclosures, MIG welding provides the speed and accuracy required for high-quality results. Our facility specialises in custom metal fabrications, offering tailored solutions to a wide range of customer specifications.
Automotive Manufacturing
In the automotive sector, MIG welding is widely used for assembling car bodies, chassis and other structural components. It allows for fast production without compromising on safety or durability.
Construction and Engineering
Steel beams, handrails, supports and stairways often rely on MIG welding during construction. Its ability to join large sections of metal quickly and securely makes it a cornerstone of modern building projects.
General Industrial Applications
From agricultural equipment to industrial machinery, MIG welding’s reliability and versatility make it indispensable in mass production and bespoke manufacturing alike.
At Cotmor, we combine MIG welding with other techniques like spot welding to ensure each project gets the best approach for its specific needs.
How MIG Welding Compares to Other Methods
While MIG welding offers many advantages, it's worth understanding how it compares to other common welding methods:
MIG Welding vs Spot Welding
Spot welding is ideal for joining thin sheets of metal together at precise points, often used in automotive manufacturing. However, it is more limited in application compared to MIG welding, which can handle different thicknesses and more complex assemblies.
At Cotmor, we often use spot welding alongside MIG welding, depending on the project requirements.
MIG Welding vs TIG Welding
TIG welding produces cleaner, more aesthetically pleasing welds, especially for delicate materials. However, it is slower and more demanding on the welder’s skill. MIG welding offers faster results for general manufacturing where volume and efficiency are priorities.
MIG Welding vs Stick Welding
Stick welding is highly portable and excellent for outdoor use, but it creates more slag and requires more cleanup. MIG welding is generally preferred for indoor manufacturing and fabrication settings due to its cleaner results and higher productivity.
Cotmor’s Commitment to Quality Welding Services
At Cotmor Tool and Presswork, based in the Midlands, we bring decades of experience to every project. Our highly trained team of welders are experts in MIG, spot welding, and a variety of other techniques, enabling us to offer comprehensive metalwork solutions.
We invest in state-of-the-art equipment and maintain strict quality control measures to ensure every weld we produce is reliable, durable, and fit for purpose.
Whether you need small, intricate metal assemblies or larger, bespoke metal fabrications, we have the expertise and capacity to deliver. We work with a wide range of industries - from automotive to construction - and pride ourselves on offering flexible manufacturing solutions tailored to your exact needs.
Thanks to our central Midlands location, we are ideally placed to serve businesses across the UK, providing fast, responsive service and dependable manufacturing support.
Partner with Cotmor for Expert MIG Welding Services
MIG welding remains one of the most efficient, versatile, and reliable methods in manufacturing today. It plays a critical role in the production of metal assemblies, metal fabrications, and countless industrial components across the UK.
At Cotmor Tool and Presswork, we are proud to offer expert MIG welding services alongside spot welding and full fabrication solutions. With a focus on precision, quality, and customer satisfaction, we’re here to help bring your manufacturing projects to life.
If you’re looking for high-quality MIG welding, spot welding, or metal fabrication services, get in touch with Cotmor today. Our experienced team is ready to support your next project with skill, care, and commitment.